江西南昌新余快速高强灌浆料联系人电话
2020-03-18 浏览次数:21次
江西南昌新余快速强灌浆料联系人电话
使用试件为单向层合板和多向层合板两种类型的玻璃纤维增强环氧树脂基复合材料层合板,采用自由落体式冲击试验机进行低能量冲击,以及**景深显微镜对损伤形貌进行特征描述。引入低能量冲击关系因子K,建立冲击能量与损伤凹坑深度量化关系,该量化关系可使冲击能量与损伤形貌特征相对应。所建立的凹坑深度与冲击能量的关系,既可以根据测量冲击凹坑深度反推出冲击时的能量值,也可以根据冲击能量预判结构的损伤情况。
△以天然橡胶为主,添加了硅橡胶、氟硅橡胶等多种橡胶相混合,保留了天然橡胶的优点,同时弥补了天然橡胶不足,所得的橡胶胶料,即具有天然橡胶的弹性好、抗撕裂性优良的优良性能,同时耐磨性、耐腐蚀性强,耐老化的特点,和常规硫化体系相结合,改善了硫化胶的耐屈挠疲劳和动态疲劳性能。
△混炼胶可以替代要求45度(邵氏)天然橡胶的橡胶定子套产品;在类似产品**使用的胶料老化性能能**30~150%。具体优点为:
●深黑色胶料,混炼胶流动性好,易于硫化加工,合格率;
△具有良好的综合性能,与金属粘结性强;力学性能、疲劳性能、耐老化等性能都较,适合生产对耐磨性能、抗老化性能要求比较的预应力施工真空灌浆料灌浆泵定子橡胶套产品。
耐磨预应力真空灌浆料灌浆泵定子橡胶套胶料及其制备方法
△橡胶硫化域,具体耐磨预应力真空灌浆料灌浆泵定子橡胶套胶料及其制备方法。
△预应力真空灌浆料灌浆泵定子橡胶套,也是预应力真空灌浆料灌浆泵中一个易损件,它的选择好坏,直接影衬套的寿命,一般正常情况下定子橡胶套的寿命为3-6个月,如果选用配方胶料不当,衬套可能从钢管中脱落或橡胶掉块。所以要求我们对橡胶胶料配方进行研究。
△灌浆料了耐磨预应力真空灌浆料灌浆泵定子橡胶套胶料及其制备方法,此橡胶胶料配方生产出的定子橡胶套,具有良好的耐热老化性、耐撕裂性,同时抗动态疲劳性能优异。
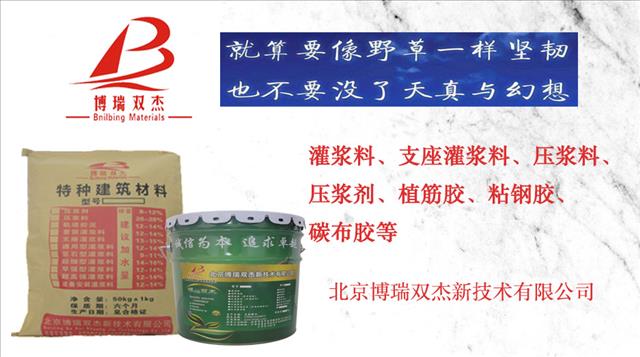
膨胀率。膨胀率是灌浆料的二个主要指标。为了使灌浆料硬化后,能够获得饱满填充效果,灌浆料必须具有适宜的膨胀性能。我国《混凝土加剂应用规范》(GBJ119-88)规定灌浆料的Id竖向自由膨胀率为0.01%0.05%,6个月的剩余竖向自由膨胀率大于0.05%。.
抗压强度。在结构加固修补中,一般都希望有较的早期强度,以便尽早投入使用。灌浆料的Id抗压强度应大于20Mpa。目前,国内常用灌浆料的抗压强度指标一般为R1N20MPa,R3N40MPa,R28N60MPa。
钢筋粘结强度无论是修补加固工程还是设备基础灌浆料灌浆,要保证灌浆料与钢筋具有足够的粘结强度,才能达到一体化灌浆料。灌浆料与光面钢筋的粘结强度一般应大于或等于6MPa,与螺纹钢筋的粘结强度一般应大于或等于30MPa。凝结时间是影响施工进度的重要指标。对于加固修补工程,往往希望强度上得越快越好,即希望终凝时间尽可能的短。但是初凝时间不易过短,过短时易造成拌合物流动性降低而影响施工操作和灌注质量。灌浆料的初凝时间一般应为lh左右,终凝时间一般应为3h左右。
目前灌浆料的基组分是:水泥、水、掺和料、加剂、砂。其主要缺点是可操作时间短,抗裂性能差,延性差。
灌浆料具有更好的流动性和更长的可操作时间、膨胀率不小于0.02%、小梁延性系数不低于■●抗压强度并可以利用废旧材料、降低成的橡胶集料灌浆料。
橡胶集料它包括以下组份:橡胶集料48份,砂6587份,水泥5585份,掺和料410份,水2032份,加剂412份,的掺和料由粉煤灰25份,硅粉12份,矿粉13份组成,的加剂由膨胀剂310份,**塑化剂12份组成,份数均为重量份数。
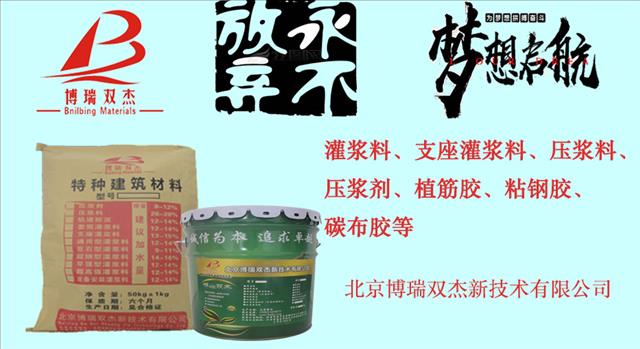
灌浆料是用途广泛的材料,它可以于大设备安装、地面自动找平、抢修工程、锚固工程、截水堵漏、补强工程等,所以不同用途的灌浆料需要具有不同的性能。如,为了加快设备的安装速度,提设备安装精度,延长设备的使用寿命,设备基础的二次灌浆料灌浆地脚螺栓的锚固等应釆用流动度大,强度和有微膨胀性的灌浆料;地面找平工程需要自流性好的中等强度的灌浆料即可;而在混凝土结构加固与修补,机场停机坪、道路、设备基础等的抢修工程中需要初凝时间调节范围大、操作性好、快硬、强的灌浆料。
解决的问题是:灌浆料无明显收缩现象产生,自流性好、不沉降、不泌水、具有塑性微膨胀性,不收缩,不产生缝隙,性能可根据用户需求随意调节调节,塑性阶段无沉缩;且具有很好的耐久性、抗油渗性、抗冻性、抗振动性,并且徐变小、脆性小,成低,使用灵活、操作简单。
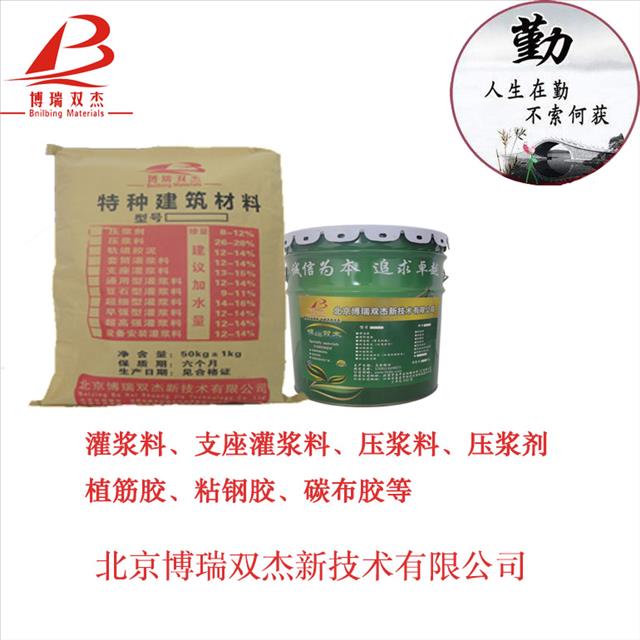
本文介绍了复合材料液体模塑成型技术(LCM)的发展历程,对发展过程中出现的一些具有代表性的工艺方法,包括树脂传递模塑(RTM)、真空辅助树脂传递模塑(VARTM)、树脂浸渍模塑(SCRIMP)、树脂膜渗透(RFI)、结构反应注射模塑(SRIM)和脉动灌注(PP)等的技术特点、研发现状及装备发展进行了回顾和总结。并对液体模塑成型工艺的发展趋势进行了展望,认为复合材料液体模塑成型工艺未来将向整体化、自动化、数字化和智能化的方向发展。
gjl36000.cn.b2b168.com/m/
使用试件为单向层合板和多向层合板两种类型的玻璃纤维增强环氧树脂基复合材料层合板,采用自由落体式冲击试验机进行低能量冲击,以及**景深显微镜对损伤形貌进行特征描述。引入低能量冲击关系因子K,建立冲击能量与损伤凹坑深度量化关系,该量化关系可使冲击能量与损伤形貌特征相对应。所建立的凹坑深度与冲击能量的关系,既可以根据测量冲击凹坑深度反推出冲击时的能量值,也可以根据冲击能量预判结构的损伤情况。
△以天然橡胶为主,添加了硅橡胶、氟硅橡胶等多种橡胶相混合,保留了天然橡胶的优点,同时弥补了天然橡胶不足,所得的橡胶胶料,即具有天然橡胶的弹性好、抗撕裂性优良的优良性能,同时耐磨性、耐腐蚀性强,耐老化的特点,和常规硫化体系相结合,改善了硫化胶的耐屈挠疲劳和动态疲劳性能。
△混炼胶可以替代要求45度(邵氏)天然橡胶的橡胶定子套产品;在类似产品**使用的胶料老化性能能**30~150%。具体优点为:
●深黑色胶料,混炼胶流动性好,易于硫化加工,合格率;
△具有良好的综合性能,与金属粘结性强;力学性能、疲劳性能、耐老化等性能都较,适合生产对耐磨性能、抗老化性能要求比较的预应力施工真空灌浆料灌浆泵定子橡胶套产品。
耐磨预应力真空灌浆料灌浆泵定子橡胶套胶料及其制备方法
△橡胶硫化域,具体耐磨预应力真空灌浆料灌浆泵定子橡胶套胶料及其制备方法。
△预应力真空灌浆料灌浆泵定子橡胶套,也是预应力真空灌浆料灌浆泵中一个易损件,它的选择好坏,直接影衬套的寿命,一般正常情况下定子橡胶套的寿命为3-6个月,如果选用配方胶料不当,衬套可能从钢管中脱落或橡胶掉块。所以要求我们对橡胶胶料配方进行研究。
△灌浆料了耐磨预应力真空灌浆料灌浆泵定子橡胶套胶料及其制备方法,此橡胶胶料配方生产出的定子橡胶套,具有良好的耐热老化性、耐撕裂性,同时抗动态疲劳性能优异。
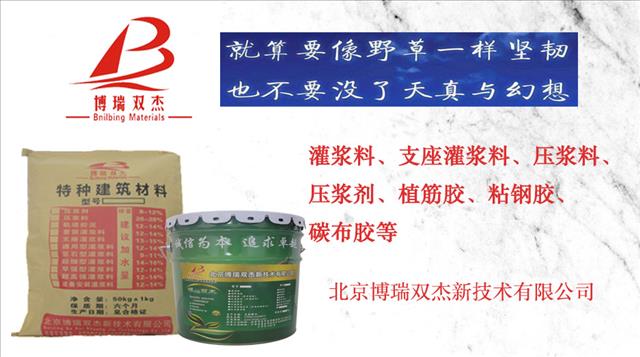
膨胀率。膨胀率是灌浆料的二个主要指标。为了使灌浆料硬化后,能够获得饱满填充效果,灌浆料必须具有适宜的膨胀性能。我国《混凝土加剂应用规范》(GBJ119-88)规定灌浆料的Id竖向自由膨胀率为0.01%0.05%,6个月的剩余竖向自由膨胀率大于0.05%。.
抗压强度。在结构加固修补中,一般都希望有较的早期强度,以便尽早投入使用。灌浆料的Id抗压强度应大于20Mpa。目前,国内常用灌浆料的抗压强度指标一般为R1N20MPa,R3N40MPa,R28N60MPa。
钢筋粘结强度无论是修补加固工程还是设备基础灌浆料灌浆,要保证灌浆料与钢筋具有足够的粘结强度,才能达到一体化灌浆料。灌浆料与光面钢筋的粘结强度一般应大于或等于6MPa,与螺纹钢筋的粘结强度一般应大于或等于30MPa。凝结时间是影响施工进度的重要指标。对于加固修补工程,往往希望强度上得越快越好,即希望终凝时间尽可能的短。但是初凝时间不易过短,过短时易造成拌合物流动性降低而影响施工操作和灌注质量。灌浆料的初凝时间一般应为lh左右,终凝时间一般应为3h左右。
目前灌浆料的基组分是:水泥、水、掺和料、加剂、砂。其主要缺点是可操作时间短,抗裂性能差,延性差。
灌浆料具有更好的流动性和更长的可操作时间、膨胀率不小于0.02%、小梁延性系数不低于■●抗压强度并可以利用废旧材料、降低成的橡胶集料灌浆料。
橡胶集料它包括以下组份:橡胶集料48份,砂6587份,水泥5585份,掺和料410份,水2032份,加剂412份,的掺和料由粉煤灰25份,硅粉12份,矿粉13份组成,的加剂由膨胀剂310份,**塑化剂12份组成,份数均为重量份数。
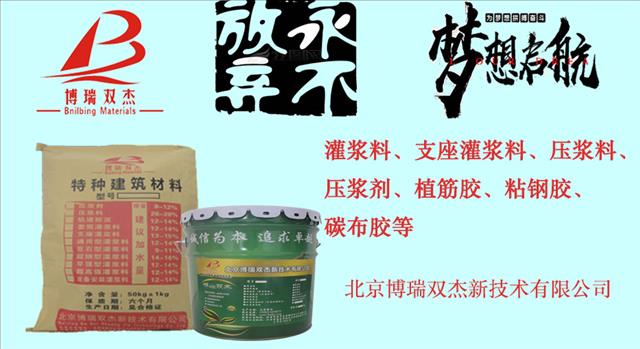
灌浆料是用途广泛的材料,它可以于大设备安装、地面自动找平、抢修工程、锚固工程、截水堵漏、补强工程等,所以不同用途的灌浆料需要具有不同的性能。如,为了加快设备的安装速度,提设备安装精度,延长设备的使用寿命,设备基础的二次灌浆料灌浆地脚螺栓的锚固等应釆用流动度大,强度和有微膨胀性的灌浆料;地面找平工程需要自流性好的中等强度的灌浆料即可;而在混凝土结构加固与修补,机场停机坪、道路、设备基础等的抢修工程中需要初凝时间调节范围大、操作性好、快硬、强的灌浆料。
解决的问题是:灌浆料无明显收缩现象产生,自流性好、不沉降、不泌水、具有塑性微膨胀性,不收缩,不产生缝隙,性能可根据用户需求随意调节调节,塑性阶段无沉缩;且具有很好的耐久性、抗油渗性、抗冻性、抗振动性,并且徐变小、脆性小,成低,使用灵活、操作简单。
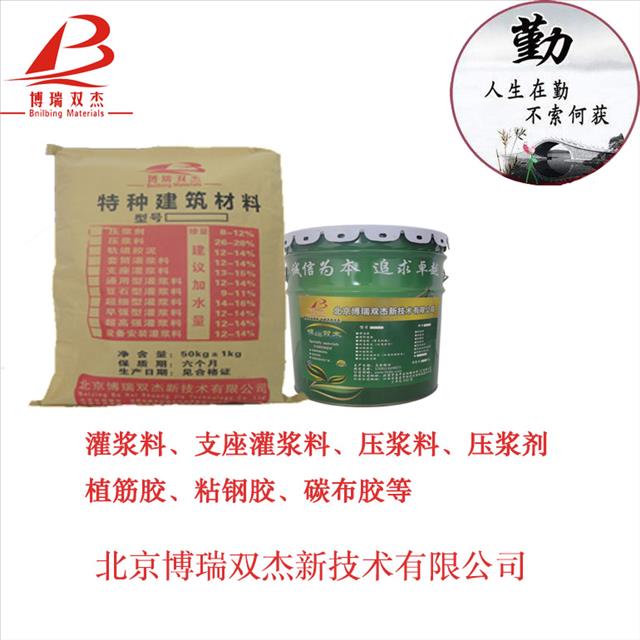
本文介绍了复合材料液体模塑成型技术(LCM)的发展历程,对发展过程中出现的一些具有代表性的工艺方法,包括树脂传递模塑(RTM)、真空辅助树脂传递模塑(VARTM)、树脂浸渍模塑(SCRIMP)、树脂膜渗透(RFI)、结构反应注射模塑(SRIM)和脉动灌注(PP)等的技术特点、研发现状及装备发展进行了回顾和总结。并对液体模塑成型工艺的发展趋势进行了展望,认为复合材料液体模塑成型工艺未来将向整体化、自动化、数字化和智能化的方向发展。
gjl36000.cn.b2b168.com/m/